Activated Carbon Pressure Filters SS
UNITEX pressure filter manufacturer offers user-friendly and ecological Vessels technologies that helps to remove a wide variety of contaminants from water based on effective water filtration with use of active carbon.
The filter is made of made of grade steel AISI316L/ 1.4404 and can be equipped with filtration system with nozzle bottom with filtration nozzles or stainless steel lateral system.
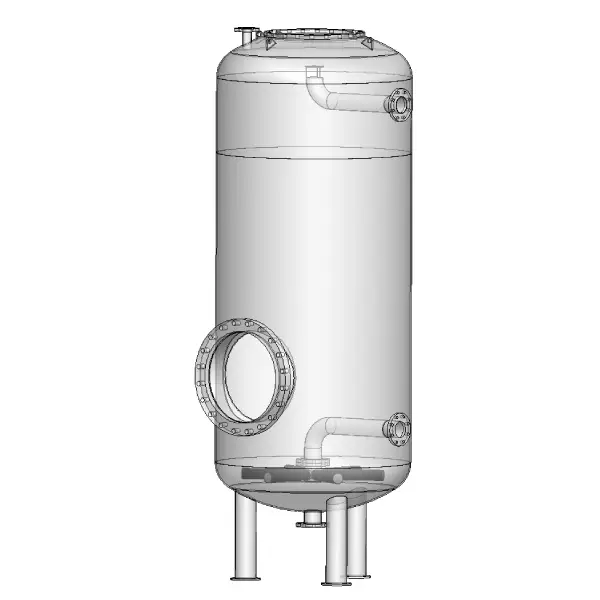
Production capabilities:
We manufacture Pressure Filters made of carbon steel in diameters from DN500 to DN4000 mm. Our designers and technologists will help to adjust pressure filters to requirements and expectations of our customers.
Ladders and platforms to support service and maintenance of the Filters:
Work safety and easy servicing of pressure filters is a very important issue. At UNITEX we make sure that our solutions are comfortable and safe for future users.
Corrosion Protection of the Pressure Filter:
An important process completing the production of stainless steel equipment is implementation 4 stages of the surface preparation process of stainless steel allows us to be certain that a ready Pressure Vessel without the risk of corrosion. Omission of any of the stages presented entails the possibility of corrosion, and thus the insufficient quality of the produced Pressure Filter. The high corrosion resistance of the surfaces prepared ensures trouble-free use of our filtres for many years.
Interior surface treatment: The process we are implementing is divided into 3 stages
- Cleaning and degreasing surfaces after production.
- Pickling – removing thermal discoloration, ferrite (rust) traces due to thermal or mechanical treatment.
- Passivation – After the passivation process, the treated product gains high corrosion resistance.
External surface treatment: The process we are implementing is divided into 4 stages
- Cleaning and degreasing surfaces after production.
- Pickling – removing thermal discoloration, ferrite (rust) traces due to thermal or mechanical treatment.
- Glass bead blasting – Mechanical surface finishing processes such as glass bead blasting/shot peening improve resistance to pitting corrosion and stress corrosion cracking.
- Passivation – After the passivation process, the treated product gains high corrosion resistance.